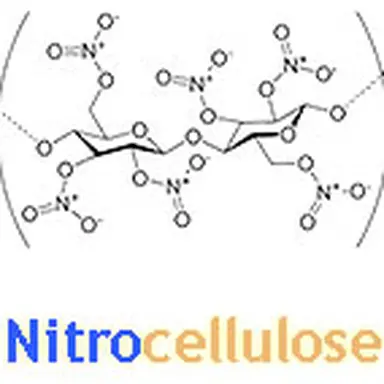
Nitrocellulose has a special place in the world of nail polish. Given its importance, but also its characteristics, it seemed useful to us to make a particular focus on this ingredient. To do this, the former technical director of one of the main manufacturers of this ingredient, SNPE (Société Nationale des Poudres et Explosifs), allows us to discover it a little more precisely. Thanks to him.
A little ancient history
Nail make-up was already known in ancient Egypt. Benzoin essences, natural resins and natural ochres were used. Industrial nitrocellulose derived from the large stocks of cotton powder at the end of World War I was used as a film-forming agent in nail polish formulations from 1920.
In 1932 Charles Revson launched the Revlon Reds range. The varnishes are then called"sedimentants" (the pigments sediment at the bottom of the bottles and small metal beads can re-homogenize the environment). In the mid-1960s,"anti-sedimenting varnishes" appeared, combining the qualities of stability and ease of application thanks to the incorporation of a rheological agent (an organophilic clay well known under its commercial name: Bentone®).
At the end of the 20th century, various regulations imposed a greater awareness of skin tolerance (elimination of toluene, formaldehyde, dibutyl phthalates, etc.). Materials of animal origin are banned, leading to reformulation with rheological agents modified by amines made from fatty substances of vegetable origin.
Manufacture of nail polishes in Bergerac
A Poudrerie Nationale (dependent on the Service des Poudres) was created in 1915 on a 200 ha site on the banks of the Dordogne. The production is the manufacture of nitrocellulose, mainly for military use for the manufacture of'gunpowder', then for the coating industries (industrial paints) and finally for the preparation of printing inks. In 1972, a civil structure was created: the S ociety N ationale des P oudres and E explosives.
It was at this time that the site's Sales Director launched the idea of developing a range of cosmetic varnishes. From the qualities used for the manufacture of inks, nitrocelluloses with high optical qualities are then produced (TX quality) thanks to : - a selection of celluloses based exclusively on cotton linters, - severe dehydration (water content less than 2.1%) - a slower manufacturing process that allows improved nitration. These nitrocelluloses will be used for the realization of the first colorless varnishes of the SNPE (ref. 306). They are suitable for obtaining transparent varnishes. They can be used to produce sedimentary varnishes, which were"the norm" at the time. This is the origin of the presence of small beads in the bottles to re-homogenize the coloured varnishes and resuspend"temporarily" the pigments that have settled in the bottom of the bottles.
In 1973, studies are carried out within the Laboratory of Studies to develop anti-sedimenting varnishes. The necessary gels are then developed on microbead mills by dispersing organophilic clays in nitrocellulose collodions. The first reference marketed is the gel 373. It is used to produce the first French antisediment varnish (ref.375X). Previously, antisediment varnishes were produced in the USA by Kirker and Durlin and imported into Europe where they were pigmented in France by Pyraline and in Belgium by Promoter.
In 1991, Pyraline, based in Melun, is bought by SNPE and its production (colourless, anti-sedimenting, coloured varnishes) is transferred to SNPE sites in Bergerac and Creysse. The SNPE range is growing. Until then, it was limited to bases for varnishes, not coloured, except for a few coloured varnishes treated under a small unit (Véronique installed in Creysse, and also from Melun).
In 1994, the production and marketing of nitrocellulose were spun off by the group and the new entity was called Bergerac NC. The nail polish department of SNPE is attached to this new entity, and continues its internationalization (started in 1989 with the acquisition of Tevco and Durlin, 2 American polish companies located in South Plainfield) with successively the following joint venture creations : - creation of Durlin Asia near Bangkok in partnership with Thai cosmetics company Thai Millot, - creation of Bergerac Japan with the Nikkol group (cosmetic raw materials) in the Toshiki province north of Tokyo, - creation of Durlin East Europ in Poland (Ciehanow north of Warsaw), - creation by Tevco in 2000 of Durlin Cosmo in Mexico (joint venture with Regio Empresas).
In August 2003, the nail polishes were separated from Bergerac NC, and production and marketing were grouped under the name Durlin France. The SNPE group thus controls an important part of the world varnish market.
Nitrocellulose of French origin and for cosmetic use represents 50% of worldwide sales of nail polishes and the SNPE group with its subsidiaries and Joint-Venture produces 30% of the nail polishes in the world.
Following the explosion at the Total site at La Grande Paroisse, near the Toulouse plant, SNPE was forced to reduce and then sell its chemical and nail polish activities. In 2010, SNPE continued its dismantling and sold its varnish production and marketing activity to Chromavis.
Nitrocellulose
It has 2 main qualities. - Energy qualities: during its decomposition (pressure in particular), a lot of heat is released in a fraction of a second. This property will be used to manufacture explosives (gunpowder, fuel casings), and ensure the needs of the military during the 1st World War). The choice of site is dictated by the presence of the Dordogne, which ensures a high availability of water necessary for the manufacturing process. - Film-forming qualities: first used in painting, then in ink manufacture (very good gloss and transparency).
Manufacturing
Nitrocellulose, the main film-forming agent in varnishes, is used as a powdery to fibrous solid (depending on grade) soaked in alcohol (mainly isopropyl alcohol). Its role is to form a flexible, shiny film that adheres to the surface of the nail. It results from nitration of cellulose by sulphonitric mixtures (sulphuric acid and nitric acid). Two parameters characterize it: the degree of substitution and the degree of polymerization.
The degree of substitution
This is the number of esterified alcohol functions per anhydroglucose group, it can vary from 0 to 3. The nitrogen rate (Dewarda method) expressed as a percentage is used to measure it.
Cellulose | Mononitrate | Dinitrate | Trinitrate | |
Degree of substitution | 0 | 1 | 2 | 2 |
Nitrogen content | 0 | 6,76 % | 11,11 % | 14,14 % |
Elemental molecular weight | 162,1 | 207,1 | 252,1 | 297,1 |
For nitrocelluloses for cosmetic use, the degree of substitution is in the order of 2.2.
The degree of polymerization
This is the number of elementary anhydroglucose links forming the polymer chain. This is the most important factor affecting viscosity. It is related to the intrinsic viscosity of nitrocellulose by a relationship of the type : viscosity] = K (DP) a where K is a polymer dependent constant and a is about 1.
Standard European viscosity | Viscosity Type Bergerac | Viscosity USA (Hercules-Aqualon) |
Soluble in esters | ||
37E 33E 30E 27E 24E 22E 19E 15E 9E 7E | E15 E20 E24 E27 E32 E35 E40 E80 E90 E110 E130 E140 E160 E220 E250 | 18-25 mPas.s 30-35 mPas.s 1/4 s 3/8 s 1/2 s 3/4 s 5-6 s 15-20 s 30-40 s 60-80 s 75-125 s 125-175 s 600-1000 s 1000-1500 |
Soluble in alcohols | ||
30A 27A 21A | A15 A20 A30 | 30-35mPa.s 1/4s 1/2s |
Depending on the raw materials used and the process used, it will have different characteristics (film-forming or energetic) and very different fields of use, paints, inks, varnishes, explosives for military use (gunpowder and combustible casings) and for civil use (airbags). In cosmetics, the typical viscosities used are in the range E15 - E35.
Table 1: Characteristics of nitrocelluloses
For nail polishes, CA4EX quality with low water content and high optical qualities (see Table 1) is used. It brings to the varnish, a very good transparency in solution, a weak retention of solvents, which supports drying. It also has the advantage of being well tolerated by the skin. The absence of residual monomers (cellulose is a natural polymer) makes it a raw material whose use is assured for the future. The nitrocellulose introduced generally corresponds to 10 to 20% of the total weight of the varnish.
Manufacturing process
The general manufacturing process of nail polishes is based mainly on mixtures of components at room temperature and dispersions of pigment particles in high stress equipment such as microbead mills.
The general production diagram can be summarized in 5 steps: - Preparation of a transparent colourless varnish - Preparation of thixotropic gel - Preparation of an antisediment base - Preparation of pigment bases - Creation of a coloured varnish
Conclusion
SNPE has made its mark on nail polish history as a producer of the main raw material. It has acquired a recognized position in the world of cosmetics thanks to the recognition of its technicality and its worldwide presence.
Contribution made by Alain Deswartvaegher After a thesis at the University of Science and Technology of Lille in 1972 on the organic synthesis of aryl tetrahydrophthalic acid derivatives, Alain Deswartvaegher was incorporated into the Scientific Service of the Army, and was assigned to the Powder Service at the Poudrerie Nationale de Bergerac. When SNPE was created, he worked in the research laboratory, in particular in charge of developing thixotropic gel for nail polish. In 1991, when the SNPE group took over, he joined the Bergerac site as development and technical assistance manager, where he was responsible for developing specific products in conjunction with the main international brands. With the R&D team, he published several patents on new bases for varnishes and the use of solvents and plasticizers of plant origin. |