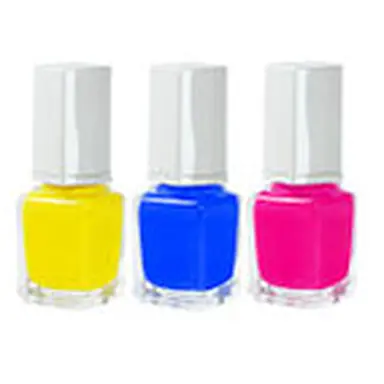
Continuation of the long history of nail polish, with its more technical aspects. After the birth of the concept and the development of this flagship cosmetic product, this time we see things from a more technical formulation angle.
See the first part of this article
Nitrocellulose as the main resin
Nail polish has changed little since its original design. The basic resin, widely used in all nail polish formulations, consists of what is called cotton nitrate, chemically nitrocellulose.
This substance has many properties compatible with its application: transparency, adhesion, semi-occlusivity, making it a versatile and almost universal ingredient in these formulations. Its limits lie mainly in its instability (flammability, explosiveness). Therefore, it is a very complicated ingredient to manufacture in the initial stages of the process. However, it should be noted that the finished products are perfectly safe to use under normal conditions of use.
Although many attempts have been made to substitute this filmogen, it continues to be the almost universal formulation basis for this family of products.
Nitrocellulose is manufactured from cotton cellulose, by direct attack of cotton balls by a concentrated sulphonitric mixture, leading to the gentle hydrolysis of the polymer, and to the integration of nitrogen in determined proportions.
Viscosity and nitrogen content will be the basic characteristics of this ingredient. Using suitable processes, the polymer is then rinsed thoroughly to remove any residual acid. The residual amount of acid will be the third parameter characterizing this ingredient. Finally, the polymer is impregnated with isopropilic alcohol to improve its stability and form the initial collodions.
Additional resins for better film quality
This basic filmogen is supplemented in commercial formulations with a filling resin to increase the dry extract and thus control the amount of film formed on the nail surface. For many years, the filling resins used were products obtained by condensation of toluene sulfonamide and formaldehyde, known under the trade name Santolite®.
This resin, which like nitrocellulose, has properties quite well adapted to its use, also has the property of releasing small quantities of formaldehyde. This has two consequences: - improve the grip of the film on the nail, formalin being a modifier of the blade (nail plate), - but also, due to its allergenic properties, to develop awareness phenomena for the use of these products.
This second characteristic led to reformulation by substitution with different complement resins. Among these, polyester resins are a widely used alternative today.
Plasticisers for film flexibility
These resins are modified by plasticizers external to the polymer, intentionally added to the formulation. These plasticizers are of two types: camphor and phthalates. The latter have been replaced for several years by a citric acid ester, triethyl citrate.
Suitable solvents
Another very important item on the form is solvents. To form a quality film, which must therefore be continuous, resins and in particular nitrocellulose, must be dissolved in a true solvent. However, only two families of solvents are compatible with this function: esters and ketones. Esters, methyl, ethyl, butyl, iso-butyl, are the most widely used, because they make it possible to obtain azeotropic mixtures with evaporation properties compatible with their use. Drying too quickly leads to flaking phenomena; if it is too long, this will lead to a film that is too soft and likely to film, and marking easily enough.
Ketones are used less frequently, mainly in quick-drying varnishes. Methyl ethyl ketone will be used in this case because acetone is too volatile.
They also form the basis for the formulation of the solvent, and acetone (dimethyl ketone) in particular. In solvents, the bleaching effect of the solvent, corresponding to the surface precipitation of proteins by the solvent, is compensated by the presence of water.
Suspension agents
The potential sedimentation of the pigments is compensated by the use of stabilizing colloids. These colloids are organophilic clays, obtained by substituting mineral cations with organic cations from common quality clays: bentonite, montmorillonite, etc.
A palette of coloured agents
Dyes are practically not used. On the other hand, pigments are those classically used and authorized in cosmetic applications.
A distinction is made between organic pigments and mineral pigments, the latter tend to favour sedimentation.
For many years, the use of so-called natural mother-of-pearl was used in formulations. These pearlescent pigments obtained from crushed fish scales, rich in guanine and hypoxanthine, allow to obtain shimmering effects.
Nowadays, these pigments are very often replaced by sandwich materials such as Mica-titanium, Silica-titanium or Borosilicate to obtain particular pearlescence and shade effects. Some specific applications include the use of particular grades of Bismuth oxychloride.
The total concentration of dyes is relatively low, in the order of 1-2%, almost always <5%.
An example of a current formulation of classic varnish: BUTYL ACETATE, ETHYL ACETATE, NITROCELLULOSE, PHTHALIC ANHYDRIDE/TRIMELLITIC ANHYDRIDE/GLYCOLS COPOLYMER, ISOPROPYL ALCOHOL, ISOBUTYL ACETATE, ACETYL TRIBUTYL CITRATE, STYRENE/ACRYLATES COPOLYMER, STEARALKONIUM HECTORITE, BENZOPHENONE-1, TRIHYDROXYPALMITAMIDOHYDROXYPROPYL MYRISTYL ETHER, ALGAE EXTRACT, DIMETHICONE, PHOSPHORIC ACID. May also contain (+/-): CI 12085 (RED 36), CI 15850 (RED 7 LAKE), CI 15880 (RED 34 LAKE), CI 15985 (YELLOW 6 LAKE), CI 19140 (YELLOW 5 LAKE), CI 42090 (BLUE 1 LAKE), CI 47005 (YELLOW 10 LAKE), CI 75170 (GUANINE), CI 75470 (CARMINE), CI 77000 (ALUMINUM POWDER), CI 77007 (ULTRAMARINES), CI 77163 (BISMUTH OXYCHLORIDE), CI 77491, CI 77492, CI 77499 (IRON OXIDES), CI 77510 (FERRIC FERROCYANIDE), CI 77742 (MANGANESE VIOLET), CI 77891 (TITANIUM DIOXIDE), MICA.
An example of a quick drying varnish formulation: ETHYL ACETATE, BUTYL ACETATE, NITROCELLULOSE, ACETYL TRIBUTYL CITRATE, PHTHALIC ANHYDRIDE/TRIMELLITIC ANHYDRIDE/GLYCOLS COPOLYMER, HEPTANE, ISOPROPYL ALCOHOL, TOSYLAMIDE/EPOXY RESIN, STYRENE/ACRYLATES COPOLYMER, MICA, STEARALKONIUM BENTONITE, N-BUTYL ALCOHOL, ADIPIC ACID/NEOPENTYL GLYCOL/TRIMELLITIC ANHYDRIDE COPOLYMER, SILICA, BENZOPHENONE-1, BENZOPHENONE-3, QUATERNIUM-18 BENTONITE, CORALLINA OFFICINALIS EXTRACT, TRIMETHYLPENTANEDIYL DIBENZOATE, POLYETHYLENE, MEK, POLYVINYL BUTYRAL, PHOSPHORIC ACID, CITRAL, ALUMINUM HYDROXIDE, DIMETHICONE, TRIETHOXYCAPRYLYLSILANE, METHICONE, TRIMETHYLSILOXYSILICATE, AQUA/WATER, LITSEA CUBEBA FRUIT OIL. May also contain (+/-) : CI 77491/CI 77492/CI 77499, CI 77891, CI 15850, CI 19140, CI 42090, CI 77510, CI 15880, CI 47000, CI 60725.
Manufacturing in several stages
The first phase consists of the manufacture of the basic polymer, nitrocellulose. This stage is carried out in very specialized chemical units, leading to which there are very few industrial operators in the world.
Resins and collodions are dissolved using high shear mixers in ADF treated premises for safety reasons.
The most complicated operation is the preparation of pigment pastes. Indeed, the dispersion quality must be optimal to guarantee a quality product.
Tinting operations are the art of the colourist and, as usual in the cosmetics industry, represent a particular stage in the manufacturing process.
Jean-Claude Le Joliff
Webography • http://www.fashion-nail.net/article-avlm-l-histoire-du-vernis-a-ongle-72885037.html • http://fr.wikipedia.org/wiki/Vernis_to_nails • http://nailartiseasy.fr/2013/01/05/lhistoire-du-vernis-a-ongles/ • http://littlemissnailpolish.blogspot.fr/2012/09/the-history-of-nail-polish-part-three.html • http://www.nailsmag.com/news/10418/nail-care-then-and-now • http://nailartjournal.com/history-of-manicure/ • http://www.beautifully-invisible.com/2011/05/nail-lacquer-blood-red-nails-fingertips-history-nailpolish.html • http://www.historyofcosmetics.net/history-of-makeup/history-of-nail-polish/ • http://www.cosmetikwatch.com/fr/produit/?id=508 • https://www.lacquerous.com/how-it-works